In the world of commercial HVAC, efficiency is a critical measurement of a unit’s effectiveness, and one (of many) methods used to improve that metric is with a hot gas reheat coil. In this article, we’ll explain the function of a hot gas reheat coil and examine the various methods used to integrate them into a unit:
- Hot gas method
- Parallel condensing method
- Warm liquid method
What is a Hot Gas Reheat Coil?
In simple terms, a hot gas reheat coil’s function is essentially its name. It uses thermal energy already in the system to reheat the airstream after it passes through the system’s evaporator. This conditions the air as it enters the space, bringing its temperature up from 50-60F to a range that’s more comfortable for occupants. The addition of a hot gas reheat coil (HGRH) eliminates the need for electric heating elements, which are often used to perform the same function.
As is true for many unit design choices, there are tradeoffs associated with the decision of whether to include a hot gas reheat (HGRH) coil in your unit. There’s an additional upfront cost, but a near-term payoff is all but certain. And, with the service lives of most units running from 10 to 15 years, the potential for meaningful cost savings exists over the life of the unit.
How do Hot Gas Reheat Coils Integrate into a Refrigerant Loop?
There are three primary methods of adding hot gas reheat to a unit, and the decision of which to use depends on preference as well as general viability with operating conditions. They are:
- Hot gas method
- Parallel condensing method
- Warm liquid method
Hot Gas Method
The first, and most common method, that we see is the hot gas method. In this configuration, refrigerant is diverted and returned in between the compressor and condenser. The refrigerant leaves the compressor as a hot gas, a portion of which is routed to the HGRH coil via a three-way valve. The remainder is routed to the condenser as it would be in a standard refrigeration loop.
The hot gas sent to the HGRH coil is then used in tandem with the evaporator to reheat cooled air as it’s ducted into the space, heating the air as it does so. A check valve is used to prevent the warm liquid from reentering the condenser.
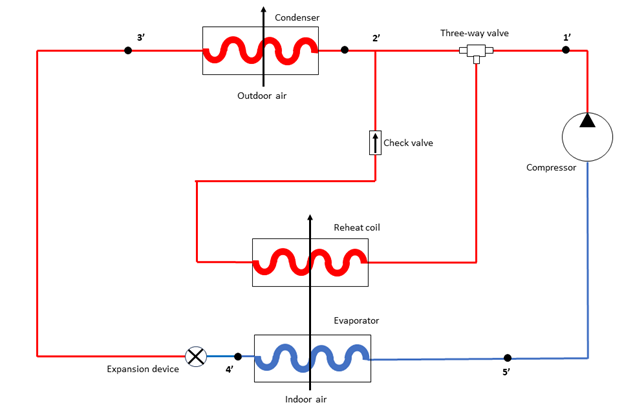
Hot Gas Method Configuration
For HGRH coils using the hot gas method, it’s important to maintain elevated refrigerant velocity to prevent the gas from condensing.
Parallel Condensing Method
This method is the second most common HGRH configuration that we see at Super Radiator. With this design, refrigerant is diverted between the compressor and the condenser coil before being returned after exiting the condenser, as illustrated in the diagram below.
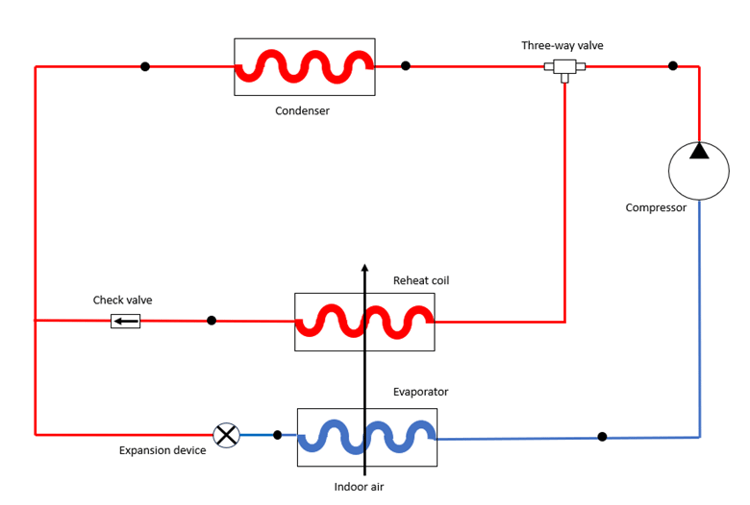
Parallel Condensing Method Configuration
The main difference between the parallel condensing and hot gas methods relates to the refrigerant’s interaction with the evaporator coil in the unit. In a parallel condensing arrangement, the refrigerant travels from the HGRH coil into the expansion device and must therefore condense completely before leaving the HGRH coil. As such, a lower flow rate is desirable, as opposed to the higher velocities needed in a hot gas configuration. Ensuring your coil is designed accordingly is critical.
Warm Liquid Method
This is a method that we rarely see, if ever, at SRC, but it is theoretically viable. In a warm liquid design, refrigerant is diverted and returned after leaving the condenser coil.
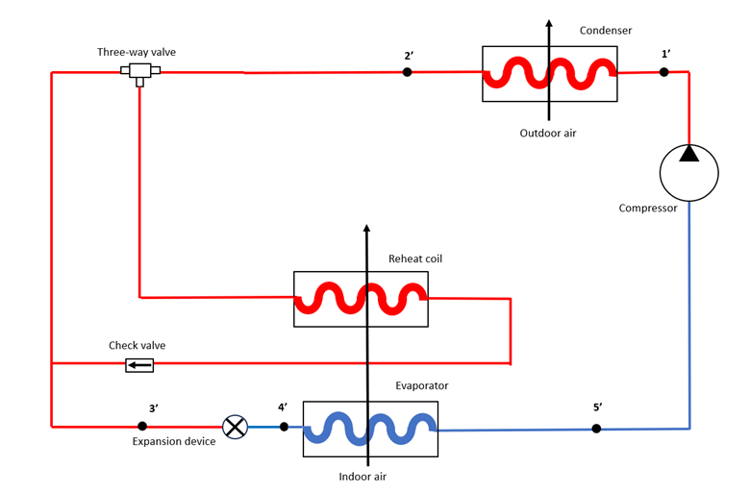
Warm Liquid Method Configuration
Unlike the other two methods, in a warm liquid configuration, the refrigerant would already be in the liquid phase upon exiting the HGRH, a dynamic that must be accounted for when calculating system flow rates and the size of the coil. However, this layout provides only a marginal performance benefit, and would therefore be very rare to see.
In summary, the addition of a hot gas reheat coil into your system presents an opportunity to lessen a unit’s electricity consumption by eliminating the need for resistance heating elements to recondition air as it enters a space. While there is an upfront cost associated with HGRH coils, it’s a cost that can usually be easily recouped in the near term, increasing efficiency over the remaining life of the unit.
If you’re an OEM looking to adjust your unit design and are considering adding HGRH, drop us a line. We can work with you to make sure you’ve got the right design method for your application and can provide some more detail on best practices when running selections in our software.
Don’t get left out in the cold when it comes to heat transfer information. To stay up to date on a variety of topics on the subject, subscribe to The Super Blog, our technical blog, Doctor's Orders, and follow us on LinkedIn, Twitter, and YouTube.