Systems designed to cool air, whether for HVAC, industrial facilities, or manufacturing operations all have to address it. Failure to address it can lead to botched processes, reduced production, ruined equipment or uncomfortable building occupants. It can be expressed in percentage, lb./lb., wet bulb temperature, or other metrics. The silent “it” is humidity. Put simply, humidity is a measure of the amount of water vapor in the air, and while overlooking this simple measure can be costly, it can also be readily addressed during system design.
Like what you're reading? Subscribe to our blog and never miss a post!
As system component engineers, we’re often asked to design a cooling coil system to cool air from a temperature – say 95°F – to a lower temperature – let’s say 55°F. The specification will show coolant requirements, whether to use cold fluid or a refrigerant, and other parameters relevant to the desired system output. Often in these specifications, a cooling load for the system is stated, usually in BTU/HR, TR, TONS, or KW. The specification appears to be complete. Even a cursory review may show that a heat balance exists for the system. This is tested by applying basic first law thermodynamics:
1.085 x SCFM x |Entering Air Temperature- Leaving Air Temperature| = Q where the temperatures are in °F.
Using this formula, the balance of the system is specified and sent for design. The Q calculate will then be used to determine the chiller size: Q= 500xGPMx∆Twater. This looks complete and solid, but is both incomplete and incorrect.
What is missing? The above equation used for determining the load, Q, does not account for the energy needed to cool any moisture contained in the air. That humidity, creates a parasitic load to the cooling system, which must be accounted for in order to properly design the system. For most cooling systems, the cooling load should be determined by this simplified form of the First Law:
Q = (4.5 x SCFM x ∆h) where ∆h = change in enthalpy of entering & leaving air BTU/Lbda
This equation accounts for the energy which may be used to cool or condense the water vapor in the air stream. This cooling load, termed the latent load, can seem invisible because it’s not seen in the temperature change of the air. Instead, the load appears in the form of condensed water vapor – condensate – on the heat exchanger. This energy can be significant and must therefore be considered. Let’s look at an example of how much energy could be involved.
For this example, consider a hypothetical system:
Airflow: 5000 SCFM outside air
Entering Air: 95°F
Desired Leaving Air: 55°F
Cooling Fluid: 45°F Water with a 10°F temperature rise through the heat exchanger
When we calculate the cooling load over a range of 0 to 100% humidity, here are the results:
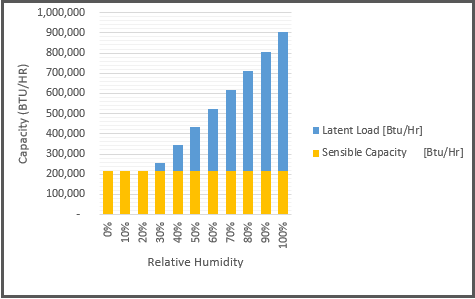
Note that when the relative humidity (RH) is 30% or greater, a portion of the cooling capacity is in the latent load. As the RH increases, a larger portion of the capacity is contained in the latent load, rising beyond 70% when the RH exceeds 80%.

When the RH is not accounted for in the system design, the result is a system capacity much less than the actual requirement. That difference between the calculated load and actual load, or shortage, can be very dramatic.
The example system operating at 70% RH has a total capacity of 618,075 BTU/HR, 401,075 BTU/HR of which is latent capacity. If the humidity were not included in the design calculations, the system would be undersized by 185%! If the example system were in a chiller plant, this is the difference between an 18-ton chiller and a 52-ton chiller. This gap would have significant impacts on budgeting, structure, utilities, and likely project feasibility.
Despite its name, the latent load is very real. All of that “lost” energy is being consumed to condense water vapor from the air. That condensing water vapor collects on the coil where it must be channeled to drainage systems and out of the cooling unit. Failure to account for this can lead to unit and facility damage.
So, how can you account for humidity's impact on the system?
The primary answer is to simply question if excluding the humidity in the specification is reasonable for the installation. If the air to be cooled is outdoor air, determine its humidity. ASHRAE Climatic Data and similar climate databases are valuable resources for historical ambient conditions. For process cooling, confirm that the load calculations have accounted for water vapor originating within the product, in addition to ambient air. Some applications may require inclusion of artificial or temporary moisture sources.
In short, if there is air to be cooled, it’s best to assume that there’s humidity to be addressed. Failing to do so at the outset of the design may have devastating effects if left unresolved. If analysis and questioning confirm that the humidity is extremely low, then the system can be safely designed without considering the humidity.
Curious about learning how humidity could be impacting your system's performance? Contact a Super Radiator engineer today.
Don’t get left out in the cold when it comes to heat transfer information. To stay up to date on a variety of topics on the subject, subscribe to The Super Blog, our technical blog, Doctor's Orders, and follow us on LinkedIn, Twitter, and YouTube.