At Super Radiator, some of our favorite projects are those that have a positive impact on the world around us. Take applications like economizers or waste heat recovery, for example. Coils designed for such purposes perform functions like harnessing otherwise wasted heat to reduce fuel costs or power other functions like heating water.
But, with some of these sorts of applications come some unique challenges. Since these applications often involve combustion – the fuel for which can take a variety of forms – accurately modeling the heat transfer properties of the resulting gas mixture (known as flue gas) requires extra care.
Flue gas mixtures – sometimes called exhaust gas – can contain several constituent substances, all with their own physical and chemical properties that must be accounted for. Unlike more ‘standard’ heat transfer applications where the working fluid’s molecular properties are very similar across most applications – like air, for example – flue gas properties can vary depending on the fuel source and the concentrations of the resulting mixture’s constituent substances.
In this post we’ll outline some engineering best practices when working with a mixed gas stream and look at a hypothetical flue gas application as an example. We’ll discuss:
- Important values & equations
- Condensing vs. non-condensing applications
- Material & design considerations
Important Values & Equations
For the example in this post, we’ll look at a flue gas application. Dozens of industrial processes require combustion, but fuel types vary. Commonly used fuels for such applications include landfill gas, biogases, and natural gas, among others. Given natural gas’s prevalence as a combustion fuel, we'll use a hypothetical natural gas flue gas for this example.
To accurately calculate the heat transfer properties of a gas mixture, we’ll need to know values for the mixture’s volume (measured in mole fraction) and its mass (measured in mass fraction).
Mole fraction is a unit that defines the ratio of one constituent’s volume (in moles) to the total moles of all substances in the mixture. I.e., this value is the amount of each constituent in a mixed gas expressed as a ratio.
The formula to determine mole fraction is: 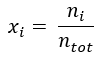
Where:
= mole fraction of a constituent
= amount of a constituent in moles
= total amount of all constituents in a mixture in moles
Mass fraction is the unit used to measure the ratio of a constituent substance’s mass to the total mass of a gas mixture.
The formula for mass fraction is: 
Where:
= mass fraction of a constituent
= mass of a constituent
= total mass of the gas mixture
Let’s look at an example using some hypothetical constituent mole and mass fractions of our flue gas. The bulk of most flue gases is comprised of some combination of nitrogen, carbon dioxide, water vapor, and oxygen. For this example, we’ll assume the constituent mole fractions of our flue gas as:
- 72% nitrogen
- 10% water vapor
- 10% oxygen
- 8% CO2
The properties of each constituent are listed below.
Constituent
|
Mol weight
|
Density (Lb./Ft.³)
|
Latent heat (BTUH/Lb.)
|
Specific heat (BTU/Lb.-F)
|
Therm. cond. (BTU/hr./Ft-F)
|
Viscosity (C-Poise)
|
Water vapor
|
18.015
|
0.04748
|
1059.32
|
0.44486
|
0.00996
|
0.00869
|
Oxygen
|
31.999
|
0.08434
|
0
|
0.21785
|
0.01867
|
0.02088
|
Nitrogen
|
28.013
|
0.07384
|
0
|
0.24901
|
0.01437
|
0.01728
|
CO2
|
44.01
|
0.116
|
0
|
0.20048
|
0.00901
|
0.01781
|
The table below shows the properties of the final flue gas mixture at three different temperatures. When comparing these two tables, you can start to see the importance of taking a granular, stoichiometry-driven approach to mixed gas stream applications. We perform these analyses on every mixed gas application we work on to make sure we’ve designed your heat exchangers for exactly the environment in which they’ll be installed.
Temp.
|
Mol wt.
|
Density (Lb./Ft.³)
|
Spec heat (BTU/Lb.-F)
|
Thermal conductivity (BTU/hr./Ft-F)
|
Viscosity (C-Poise)
|
60˚F
|
16.71921
|
0.04264
|
0.50567
|
0.01811
|
0.01109
|
124 ˚F
|
16.71921
|
0.03796
|
0.52434
|
0.02069
|
0.0123
|
145 ˚F
|
16.71921
|
0.03665
|
0.53136
|
0.02158
|
0.01268
|
Condensing vs. Non-Condensing Applications
When designing heat exchangers for use with flue gas, accounting for the presence of water vapor in the gas mixture is imperative, which is why we’ve highlighted it above. In applications where that vapor condenses, failing to account for the latent load it creates could lead to significant issues like undersized heat transfer equipment.
Another issue that can arise from improperly managed water vapor is corrosion, especially if the flue gas is being cooled below the water vapor dew point. At this point water condenses and mixes with the flue gas, which can lead to the formation of acidic compounds that can attack the coil. Even if you are cooling your flue gas above the water dew point, the surface temperature of the coil's tubes may still be colder than the dew point, at which point localized condensation can occur. Facilities managers should consider this fact when deciding on material selection for heat transfer components.
Material and Design Considerations
For example, an unprotected copper and aluminum heat exchanger would likely corrode if installed in an environment like the one described above. Because of this, many of the products we design for such applications are built with stainless steel. Stainless coils have larger footprints and higher cost, but ample service lives when properly maintained and operated.
If a stainless steel design is cost prohibitive, there are several coating options that can help bridge the gap between cost and corrosion resistance. Read our blog to learn more about some different coating options, their tradeoffs, and some suitable applications for each.
And if you’re looking for help designing heat transfer equipment for a mixed gas stream, drop us a line. Whether you’re using biogas, landfill gas, natural gas, or some other combustion fuel, we can help engineer a heat exchanger that’s designed for your exact application – down to the molecule.
Don’t get left out in the cold when it comes to heat transfer information. To stay up to date on a variety of topics on the subject, subscribe to The Super Blog, our technical blog, Doctor's Orders, and follow us on LinkedIn, Twitter, and YouTube.