This article has been updated. It is accurate as of 9/23/20.
Heat exchangers used for different applications need different design features. For example, in industries like pulp and paper, lower fins per inch (FPI) are often included to reduce airside fouling and to make for easier cleaning. Other applications such as the military are often concerned with weight, which impacts material selection. For this post, we're going to focus on some unique design choices we often include when building heat exchangers for the refrigerated storage of potatoes, onions, beets and other vegetables.
Potato storage facility in the Northwest
1. Compatibility for end user customization
Often, cooling systems in commercial agriculture storage warehouses operate at temperatures just above freezing to prevent spoilage. Because of these low temperatures as well as humidification, frosting on coils is a real concern, and many facilities use electric heating elements to the keep evaporators free of ice and frost. Knowing that, we design our coils to include heater notches to accommodate these devices.
Customers have three design options if heater notches are needed. The first involves using a special die that punches heater notches into the fins themselves like in the video above and the image below. We can also use strategically placed dead tubes in the coil to accommodate the heaters, or we can opt for a split fin pack, designed with two fin packs built into one casing with enough space between the two to fit the heaters.
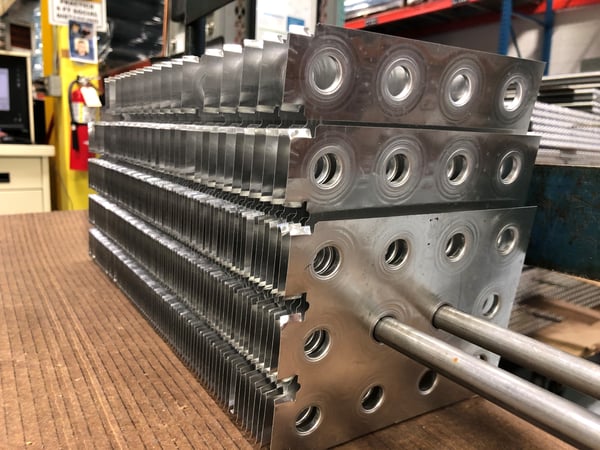
2. Clean and cleanable equipment for contaminant-free food
We fully degrease our products using a vaporized degreasing solution prior to shipping them out to our customers. This way, customers receive a heat exchanger that’s clean, ready to use, and free of contaminants.
Like what you're reading? Subscribe to our blog and never miss a post!
While our coils start clean, we know they won’t stay that way for very long in the field. Given the presence of dirt and other particulates, coils for agricultural storage applications need to be designed for easy cleanability in the field. Design choices like thicker fin gauges to withstand pressure washing and increased spacing between fins helps make life easier for end users when it comes time to clean their equipment, allowing them to clean coils off without removing them from service. Lower FPI also helps to minimize the frosting concerns mentioned earlier.
3. Corrosion resistant products to reduce frequency of replacement
Given the presence of a number of chemical and environmental corrosives like ammonia from fertilizers, the use of coatings is common in the industry. E-coat, or electrocoating (pictured below) is popular in the industry both because it’s thin - roughly 1 mil dry film thickness - and results in a less than 1% reduction in heat transfer. Additionally, when paired with a hydrophobic topcoat, condensate water – often containing chemicals – is beaded off of the fins, further decreasing contact with equipment and reducing the opportunity for corrosion.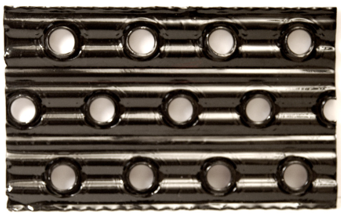
Another option would be fin stock that's pre-coated with a blue corrosion-resistant lacquer, like the kind used in the condenser pictured below. Unlike the post-build coatings discussed above, pre-coated fin stock only protects fins and would be well suited for environments in which corrosives exist in the airstream but less so on the fluid side. Pre-coated fin stock is a cheaper alternative to the above coatings, but it's also less robust and therefore not best suited for environments with aggressive corrosives.
A third option is Heresite P-413, a baked-on phenolic coating designed to offer robust protection to a multitude of acids, solvents, and inorganic salts. This chemical resistance comes from its high cure temperature and unique chemistry, and, as a result, Heresite P-413 is a popular option for applications like commercial crop storage. Like e-coat, Heresite P-413 provides a heat transfer reduction of <1%. Its dry film thickness is similar as well, at around 1 mil.
All applications are different, though, with some needing far less investment in coatings and others needing much more. A variety of resources exist - on this blog and other sites - to help determine the best coating package for a given application.
4. High-quality braze joints for continuous leak-free operation
Our brazing program is critical to what we do at Super Radiator Coils. All of our brazers are certified under ASME section IX code, our rigorous internal standards, as well as any standard requested by the customer. The result is high quality braze joints every time, regardless of the materials being used.
For example, when making evaporators, our brazers have the ability to use braze rod with a wide range of silver content - from as little as 0% silver to as much as 45% or more if requested. Braze rod with higher silver content is less runny, and affords the brazer greater control during the brazing process. And, although we don't have corroborating testing data, it's generally thought in the industry that higher silver content results in a more ductile joint, and therefore one that's less susceptible to the effects of forces like shock and vibration. Then, we fully test our coils with dry nitrogen prior to shipment to ensure that our work meets our standards and won't leak in the field.
Braze rod with higher silver content also allows our brazers to more easily join dissimilar metals, expanding the material combinations we're able to use, and increasing the likelihood that we can make exactly the part you're looking for.
Do you rely on heat transfer for any agricultural storage applications and want to know if using these coil designs could help improve your efficiency? Give us a call today.
And check out the links below for some more articles from our Application Spotlight series.
Don’t get left out in the cold when it comes to heat transfer information. To stay up to date on a variety of topics on the subject, subscribe to The Super Blog, our technical blog, Doctor's Orders, and follow us on LinkedIn, Twitter, and YouTube.