We get asked a lot of questions about the passivation of stainless steel welds. Oftentimes, customers want to know what passivation is. Others ask if it’s necessary. Given the number of factors that such a decision hinges on, Super Radiator wants customers to understand the benefits of passivation, and also understand what’s involved in the larger process of treating stainless steel surfaces.
For this post, we’ll discuss some types of stainless steel surface treatment, explain their purposes, and outline some popular methods of achieving a passive surface following welding.
What purposes do stainless steel treatments serve?
To answer this question, it’s first important to know some of the characteristics of stainless steel. Stainless steel is an iron-based alloy that contains a minimum of 10% chromium (Cr), and is classified using four families according to their properties and microstructures:
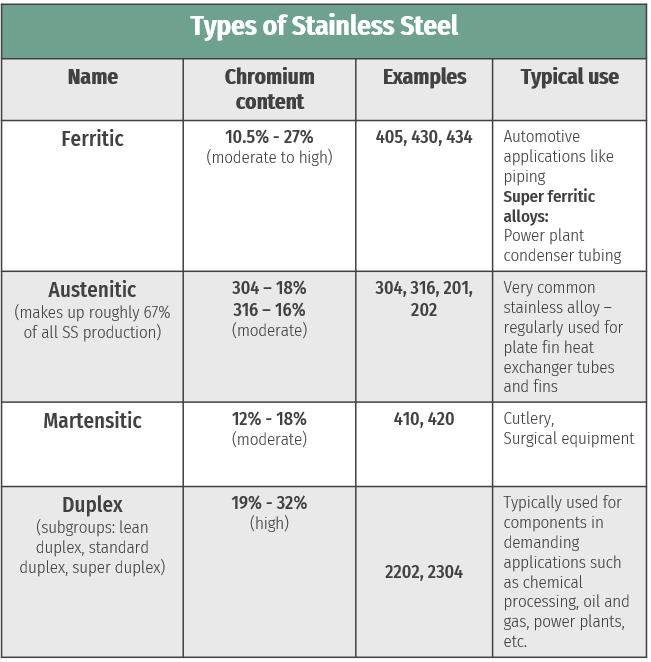
Like what you're reading? Subscribe to our blog and never miss a post!
Stainless steels owe their corrosion resistance properties to the presence of chromium, which varies depending on type of stainless, but is present in all varieties. Once that chromium reacts to oxygen under normal atmospheric conditions, a thin but strong passive layer of chromium oxide is created. This passive layer is just that – passive, meaning that it inhibits reactivity, preventing the occurrence of reactions such as oxidation, also known as rust formation.
There are a number of stainless steel surface treatments meant to develop or enhance the steel’s passive layer. Those processes are descaling, pickling, and passivation.
These processes all have to do with some manner of either establishing or accelerating the establishment of the passive layer, or some other method of chemically treating steel so as to rid it of contaminants without interrupting the naturally occurring passive layer. Some examples of such contaminants are free iron, oxide scale, rust, grease, oil, carbonaceous or other residual chemical films, soil, particulate matter, metal chips, or dirt.
However, oftentimes these three processes are conflated. While similar, they aren’t identical, even though each serves as an individual step of a larger stainless steel surface treatment process. It should be noted that the cleanliness of the stainless is an important factor throughout the following processes, as oil, grease, and other contaminants can make for poor coverage or spottiness.
Descaling:
This is the process of removing any thick, visible oxide scale from the steel’s surface. This is typically done during the steel-making process and can be done through mechanical cleaning or an acid cleaning process.
Pickling:
Pickling is similar to descaling but is considered a separate process. It consists of chemically removing the layer of the steel that was exposed by the descaling process. This is accomplished using any number of nitric and hydrofluoric acid mixtures and removes imperfections that result from industrial processes such as weld tint.
Passivation:
Passivation will occur naturally over time, but manufacturers frequently look to accelerate that process through the use of chemical agents, such as nitric or citric acid. This is known as acid-assisted passivation. Unlike pickling, this method of passivation doesn’t remove any base metal from the steel’s surface, rather it dissolves surface impurities, and accelerates the natural formation of the steel’s chromium oxide layer, given that an adequate oxygen concentration is present.
What are some methods for passivating stainless steel?
There are a few different methods for passivating stainless steel, including chemical baths as well as brush-on and spray-on applications.
Nitric acid/citric acid passivation: For types 304 and 316, whose chromium content is typically between 15 and 23 percent, there are two common types of acid baths. The first involves submerging the item in a 10% by weight citric acid solution for 30 minutes at 150°F. Another option is to use a 20% by weight nitric acid solution for 30 minutes at 120-140°F.
Specialized tools: A third option is a number of commercially available tools designed for treating stainless surfaces following welding, specifically. We employ this method at Super Radiator, specifically the TIG Brush, which uses an adjustable probe to apply a combination of electricity, chemistry, and heat to the steel’s surface, thereby reestablishing the passive layer after welding. A major benefit of this method is efficiency, as the TIG Brush both cleans oxide scale off welds and passivates the steel in one pass.
Ultimately, the decision of whether to passivate stainless steel coils is at the customer’s discretion. However, if corrosion resistance is a priority and passivation isn’t cost-prohibitive, it would make a lot of sense to opt for it.
At Super Radiator, we have in-house stainless experts who can provide guidance and recommendations when deciding whether to passivate stainless coils. We consider stainless passivation a best practice, as it ensures maximum corrosion resistance of a relatively expensive material, thereby increasing the lifespan and durability of the product.
Don’t get left out in the cold when it comes to heat transfer information. To stay up to date on a variety of topics on the subject, subscribe to The Super Blog, our technical blog, Doctor's Orders, and follow us on LinkedIn, Twitter, and YouTube.