In many of the industries we serve, heat exchangers made with copper tubes and aluminum fin are extremely popular, and very often, these materials are a terrific choice. But copper and aluminum aren’t suited for everything. At Super Radiator Coils, the needs of many of our customers often dictate that we explore and understand alternative materials.
For this post, we’ll outline four materials that we use for fins, tubes, and headers when aluminum and copper aren’t the best choice – usually because of some combination of high temperatures, high pressures, or corrosion concerns. We’ll give an overview of each, the pros and cons of their respective properties, and some applications for which they’re commonly used.
- Stainless steel and stainless super alloys
Pros: corrosion resistance, durability, temperature and pressure tolerance
Cons: poor to moderate heat transfer performance, cost
All three of our plants use stainless steel for everything from tubes to headers, fins and casings. The real benefit of stainless steel comes from its chromium content, which makes the metal resistant to corrosion.
Stainless alloys can contain any number of elements, but they all contain a minimum of roughly 11% chromium, which forms a passive layer when exposed to air, making stainless steel very resistant to uniform corrosion attacks. As a rule of thumb, the higher the chromium content, the more resistant the stainless is to uniform corrosion.
That’s not to say that stainless is altogether impervious to corrosion. At high enough concentrations, strong acids like hydrochloric acid can corrode stainless, as can basic solutions like sodium hydroxide.
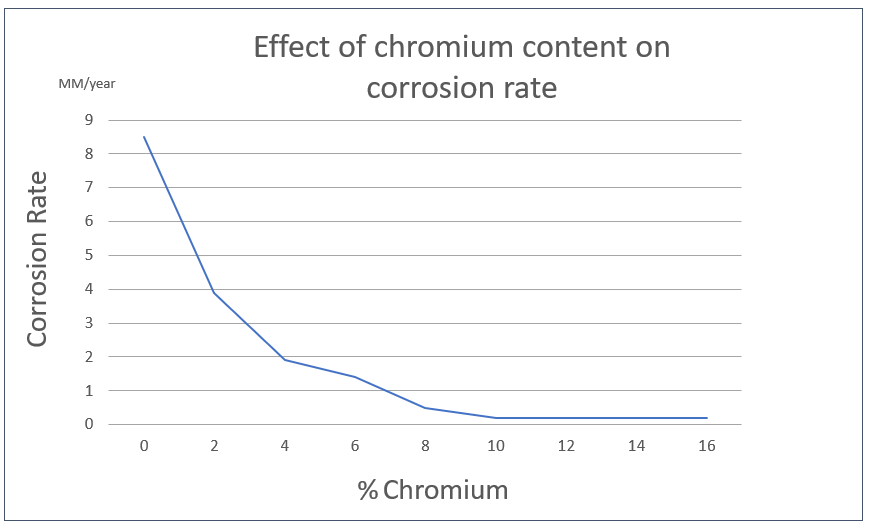
Source: "Design Guidelines for the Selection and Use of Stainless Steel"
Types 304 and 316 are among the most common stainless steels, both at SRC and for steel consumers everywhere. These types of stainless are workhorses for a number of industries, including water treatment, oil and gas, food processing, and many others.
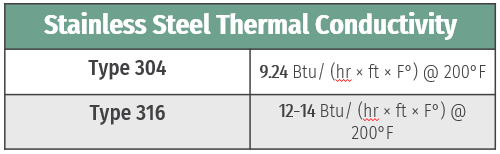
While stainless steel’s resistance to corrosion is very good, its heat transfer performance is a drawback, as all stainless steels are poor to moderate conductors of heat. Their thermal conductivities range from 8.1 Btu/ (ft. hr. °F) for super-austenitic alloys to 15.1 Btu/ (ft. hr. °F) for ferritic alloys. While stainless steel’s conductivity is on the lower end, it’s typically used for applications in which excellent heat transfer is a lower priority than things like tolerance to high temperatures, pressures, and corrosion.
For a comparison of the heat transfer performance of these materials, we’ll use a hypothetical heat exchanger – a 40” x 80” water coil. The capacity (Btu/Hr.) of that coil built with 304 stainless steel tubes and aluminum fins is 19% less than the same coil made using copper tubes.
Stainless steels are grouped into four categories based on their crystalline structure: ferritic, austenitic, martensitic, and duplex.
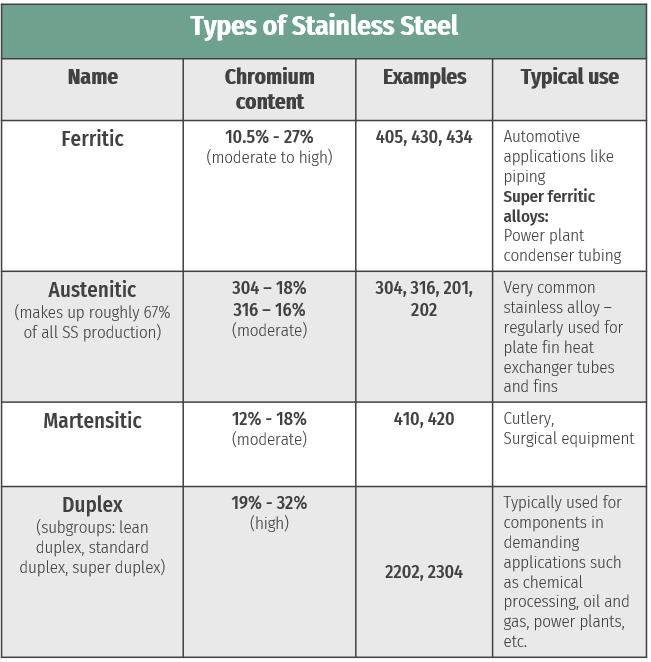
The corrosion resistance of stainless steels is further bolstered by molybdenum, the addition of which enhances resistance to pitting corrosion. Nickel is a frequent ingredient in stainless alloys too. One material with elevated levels of those elements is AL-6XN®, a super-austenitic stainless alloy that we regularly use to build heat exchangers destined for highly acidic, polluted, or saline environments.
Like what you're reading? Subscribe to our blog and never miss a post!
Its composition is in the table below. AL-6XN also contains small amounts of other elements such as nitrogen, phosphorous, and manganese, which enhance the steel’s hardness and contribute to its corrosion resistance.
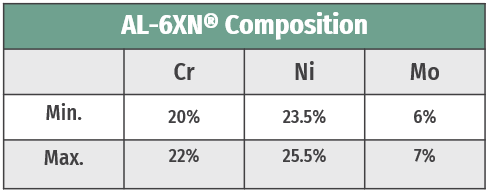
Another super-austenitic stainless steel that we use for its top-tier resistance to corrosion is Hastelloy®. A number of corrosion-resistant and high-temperature alloys are sold under the Hastelloy name, with C-22® being among the most popular. Known for its resistance to both oxidizing and non-oxidizing substances, Hastelloy® C-22® is often used in harsh industrial environments.
- Cupronickel
Pros: Corrosion resistance, durability, heat transfer
Cons: cost
Cupronickel, or copper-nickel, is a copper alloy containing nickel, as well as elements to improve strength, like iron – which also adds resistance to high flow rates – and manganese, which functions as a deoxidant during mixing and casting. The addition of nickel makes cupronickel resistant to corrosion, specifically against seawater in marine environments. Its copper content typically varies from 60 to 90 percent, but we most commonly see cupronickel in 90/10 and 70/30 alloys, named for their copper to nickel ratios, respectively. See the breakdown of those two alloys below.
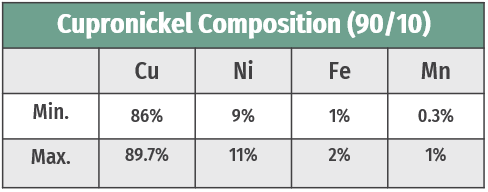
Cupronickel owes its corrosion resistance to the thin, adherent protective surface film that develops quickly after exposure to clean seawater. This takes roughly two to three months to fully form, after which corrosion rates will continue to decrease over time.
Cupronickel alloys are slightly better conductors of heat than stainless steels, with a typical range of 29 Btu/(hr × ft × F°) at 200°F for 70/30 cupronickel to 33 Btu/(hr × ft × F°) at 200°F for the 90/10 variety. Of the metals covered in this piece, cupronickel’s heat transfer performance is second to only that of copper. If we use the same hypothetical coil from the previous section, the capacity (Btu/Hr) of a 40” x 80” cupronickel water coil with aluminum fins is only 9% lower than a copper/aluminum version of the same coil.
Cupronickel’s terrific corrosion resistance is its chief benefit, making it ideally suited for marine applications, such as desalination plants and offshore oil and gas platforms. Other common cupronickel applications include power station condensers, steam generation for the shipping industry, and in components of heat recovery systems in desalination plants, among others.
- Carbon steel
Pros: Heat transfer performance, strength, versatility, heat tolerance, cost
Cons: Poor corrosion resistance
The third material this piece will cover is carbon steel. Named for its carbon content, carbon steel is classified according to the same criterion: low carbon steel, medium carbon steel, and high carbon steel. Carbon steel typically contains .04% to 1.5% carbon content. Other elements are often added to improve desirable characteristics like hardness and weldability.
We mostly use mild steel for heat exchangers mostly for its weldability, but also partially due its thermal conductivity, which, at an average of roughly 26 Btu/(hr × ft × F°) at 200°F , places it squarely in the middle of metals covered in this post. For example, our theoretical 80 x 40 water coil made using carbon steel results in a 16% capacity reduction relative to a copper coil of the same dimensions.
Like stainless steel, carbon steel is also valued for its ability to operate in higher temperature applications than copper.
- Titanium
Pros: Strength, corrosion resistance
Cons: Poor heat transfer performance, cost, availability, lead time, workability
The last metal this piece will examine is titanium. While we don’t work with it frequently, every so often customers request it, or our engineers determine it’s a suitable option based on the operating environment.
Titanium’s benefit comes from its strength and corrosion resistance. It’s extremely strong, making it well suited to industrial environments. In its non-alloyed form, titanium’s strength is similar to that of steel, while also being much less dense than steel, so it’s worth considering if weight is an important factor.
When we work with titanium, we tend to use two types: Grade 1 (per ASME SB-338) and Grade 2 (per ASME SB-861), both of which are unalloyed a.k.a. "commercially pure." Grade 1 is on the lower end of the strength spectrum as far as titanium goes. It’s also the softest and most ductile of the unalloyed titanium varieties. Grade 1 also offers good cold formability and impact toughness along with titanium’s excellent resistance to corrosion. Because of these properties, we use grade 1 titanium tubes when building titanium heat exchangers.
Grade 2 titanium is known as the “workhorse” of titanium. Its cold formability and relative ease of fabrication make it desirable for a number of applications such as power generation, pulp and paper, and food processing. Grade 2 also possess good weldability and excellent corrosion resistance. When we need to make titanium headers, we use grade 2.
Heat transfer-wise, titanium falls on the lower end of the spectrum, with a thermal conductivity of roughly 12 Btu/ (hr × ft × F°) at 200°F. Titanium is sometimes seen in similar applications as stainless and cupronickel, such as marine systems, water desalination, and power generation.
Refer to the chart below for a comparison of the thermal conductivity of all the metals covered in this post, along with copper for comparison purposes.
In summary, there are a bevy of material options out there outside of copper and aluminum, and there are nearly limitless material combinations possible for heat exchangers. The experience of our engineers combined with our coil selection software means we can design a coil using any of the materials covered in this post. If you’re unsure of what materials your application needs, but don’t think copper and aluminum are the right choice, give us a call. We’ll design you a coil that meets your needs and agrees with your budget.
Don’t get left out in the cold when it comes to heat transfer information. To stay up to date on a variety of topics on the subject, subscribe to The Super Blog, our technical blog, Doctor's Orders, and follow us on LinkedIn, Twitter, and YouTube.