Stainless, copper, E-coat, Heresite, or CuNi?
When Super Radiator Coils engineer coils for customers, materials are among our most important considerations. Things like applications, environments, and coil lifespan must all be factored in to the coil’s design. So too must price and industry standards, making material decisions all the more crucial.
Unlike light commercial applications, where planning and decision-making occur over weeks or months, industrial projects tend to move at a much slower pace, with project timelines often spanning months or years.
With industrial projects, quality and lifespan are often chief concerns. Therefore, these projects may involve considering different materials than those used in a typical commercial HVAC application.
For this post, we’ll take a look at five examples of fins made from materials one might see on an industrial heat exchanger. We’ll examine the relative cost, heat transfer performance, and corrosion resistance of each. For cost comparison purposes, all fins will be ranked from most expensive to least expensive.
Like what you're reading? Subscribe to our blog and never miss a post!
Option 1: Copper nickel fins
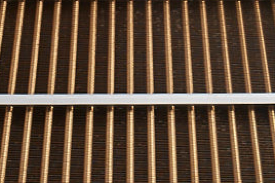
Cost: 1
Thermal conductivity: Copper nickel’s heat transfer capability varies depending on the alloy. The two main copper nickel alloy grades are 90/10 and 70/30 copper and nickel, respectively. Their thermal conductivity typically ranges from 17 Btu/hr × ft × F° to 23 Btu/hr × ft × F°[i].
Corrosion resistance: Copper nickel is very resistant to seawater corrosion and is often used in industrial marine environments because of that reason. This resistance is due to the formation of a thin, adherent protective surface film that develops quickly after exposure to clean seawater. This coating takes roughly two to three months to fully form, after which corrosion rates will continue to decrease.
Takeaways: It’s the most expensive material covered in the piece and its heat transfer is at the lower end, but its durability and corrosion resistance make it well suited for a bevy of industrial applications, especially in marine environments.
Option 2: 316 stainless steel fins
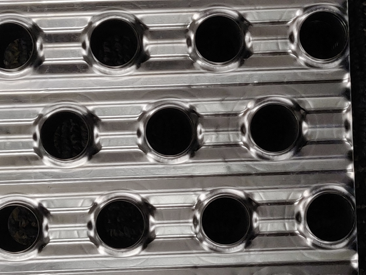
Cost: 2
Thermal conductivity: The heat transfer capability of 316 stainless is relatively poor. While better than type-304, 316’s is still only between 17 Btu/hr × ft × F° and 13 Btu/hr × ft × F°, which is at the lower end of the spectrum covered in this piece.
Corrosion resistance: Unlike type-304, 316 stainless contains molybdenum, which helps provide greater corrosion resistance against things like localized attack by chlorides as well as general corrosion from reducing acids like sulfuric acid. Thus, type-316 is typically used in harsher corrosive environments than 304.
Takeaways: Type-316 stainless is tough and durable, capable of withstanding harsh industrial environments. However, its relatively poor heat transfer capability makes it best suited for environments where resilience and lifespan are more valued than heat transfer.
Option 3: 304 stainless steel fins
Cost: 3
Thermal conductivity: Like type-316, poor heat transfer is among the largest drawbacks of using stainless for heat exchangers. Its heat transfer capability (9.24 Btu/(hr × ft × F°[ii]) is worse than aluminum (136 Btu/hr × ft × F°[iii]) and far worse than copper (231 Btu/hr × ft × F°[iv]).
Corrosion resistance: Stainless provides excellent corrosion resistance and is a great choice if corrosion mitigation is an application’s primary concern. Due to its chromium content, stainless undergoes passivation in wet environments, which forms a thin inert surface film of chromium oxide when exposed to even small amounts of oxygen. The film inhibits additional corrosion by blocking oxygen diffusion to the surface of the steel, which prevents corrosion from spreading.
As far as corrosion from acids and bases, room temperature 304 stainless is only resistant to 3% acid and may not be a practical choice for acidic environments. 304 can also be susceptible to crevice corrosion by chlorides.
Takeaways: Performance is similar to 316, but 304 is less corrosion resistant.
Option 4: Copper fins
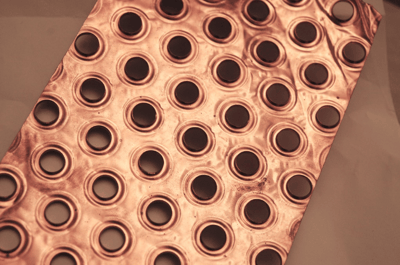
Cost: 4
Thermal conductivity: Copper is among the most thermally conductive substances on Earth, making it extremely effective in heat exchangers. At 231 Btu/hr × ft × F°, copper’s thermal conductivity rating is 60% greater than that of aluminum and 3,000% that of stainless.
Corrosion resistance: In clean air, water, and deaerated non-oxidizing acids, copper corrosion occurs at very low rates. However, in harsher environments, copper oxidizes over time, resulting in a green patina. This patina protects the copper from corrosion to a certain degree, but not from aggressive corrosives like acid rain.
Takeaways: Uncoated copper fins likely aren’t feasible for most harsh industrial environments, especially acidic ones. However, if heat transfer is the top priority and the coil’s application doesn’t involve acids, copper fins are a very good option.
Option 5: Heresite P413-coated aluminum fins
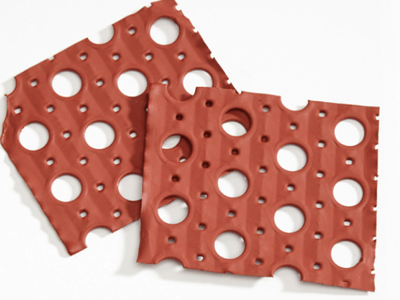
Cost: 5
Thermal conductivity: Coating aluminum fins with Heresite has a less than 1% negative effect on a coil’s heat transfer capabilities. It’s effectively the same as non-coated aluminum and copper. Heresite is a good option for applications that want the heat transfer benefits of copper or aluminum, but with far greater resistance to corrosives.
Corrosion resistance: Heresite provides terrific corrosion resistance and can tolerate a multitude of corrosive atmospheres. It’s particularly effective in coastal and marine salt air applications, having passed 1,000 hours on the ASTM G85-A3 Acidified Synthetic Sea Water Testing (SWAAT) test. Heresite also meets the ISO 12944-9 (formerly ISO 20340) standard, having withstood 4,200 hours (25 cycles) alternating between salt spray, UV radiation, and temperature shocks. Heresite is the first HVAC-R and radiator coating to meet this standard.
Takeaways: Heresite-coated aluminum fins are suitable for a variety of options. For applications where price, heat transfer, and corrosion resistant are all equally valued, Heresite should be considered, especially for marine and salt air environments.
Option 6: E-coated aluminum fins
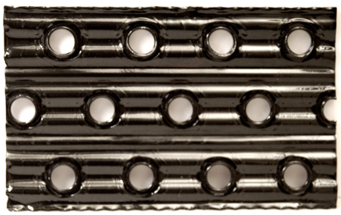
Cost: 6
Thermal conductivity: Like Heresite, e-coat reduces heat transfer by less than 1%, with little difference between a coated coil and a bare one as far as heat transfer goes.
Corrosion resistance: E-coat also provides terrific corrosion resistance, having passed 3,000 hours on the ASTM G85-A3 (SWAAT) test. E-coat has not been tested against the ISO 12944-9 standard.
Takeaways: Like Heresite, E-coated aluminum fins are a good option for a variety of applications, such as coastal areas, or industrial environments with high humidity and aggressive atmospheres like power plants, refineries, or steam turbines.
Don’t get left out in the cold when it comes to heat transfer information. To stay up to date on a variety of topics on the subject, subscribe to The Super Blog, our technical blog, Doctor's Orders, and follow us on LinkedIn, Twitter, and YouTube.
[i] https://www.copper.org/applications/marine/cuni/properties/physical/
[ii] https://www.azom.com/properties.aspx?ArticleID=863
[iii] https://www.engineersedge.com/properties_of_metals.htm
[iv] https://www.engineersedge.com/properties_of_metals.htm