Are you getting the most out of your steam system investment? Steam has been used as a heat transfer medium for centuries. Today, it remains a popular option for commercial heating and a multitude of industrial applications. But, in our experience, the industry’s understanding of steam and steam equipment is inconsistent, and we’re hoping to help make things a little clearer as it relates to the following areas.
-
Types of steam coils
a. Standard steam coils (single-pass & multiple-pass)
b. Steam distributing coils (single-pass)
-
Steam coil design best practices
a. Coil construction (plate fin vs. spiral wrap)
b. Tubes
-
How SRC and KEI can help you optimize your steam system design
Types of Steam Coils
In the work we do at SRC, steam coils take one of two forms: a steam coil – also known as a standard steam coil – or a steam distributing coil.
Standard Steam Coils
A standard steam coil, or simply a steam coil, is a heat exchanger that uses steam to heat air or another gas. Steam is supplied to the coil via an inlet header, which is then distributed throughout the coil in a series of tubes like you’d find on most coils.
As air passes across a steam coil’s fin surface, it absorbs the thermal energy emanating off it. The heated air then mixes with downstream air, raising its temperature to the application’s specification.
Single-Pass Standard Steam Coils
This type of steam coil design is the more flexible of the two designs. They’re less complex and are typically a first option. Some important things to know about single pass standard steam coils are:
-
Single-pass steam coils feature a steam inlet header on one end of the heat exchanger with a condensate outlet header on the opposite end.
-
Steam coils are usually 1, 2, or 3-row designs. The steam makes a single pass through the coil’s straight tubes, entering at the steam inlet header and exiting the tube through the outlet header on the opposite end.
-
Single-pass steam coils are the most common design for non-modulating (constant volume & temp.) steam applications. They can be mounted in either a horizontal or vertical orientation as seen below. When mounted horizontally, the tubes should be pitched in case configuration for proper draining of the condensate.
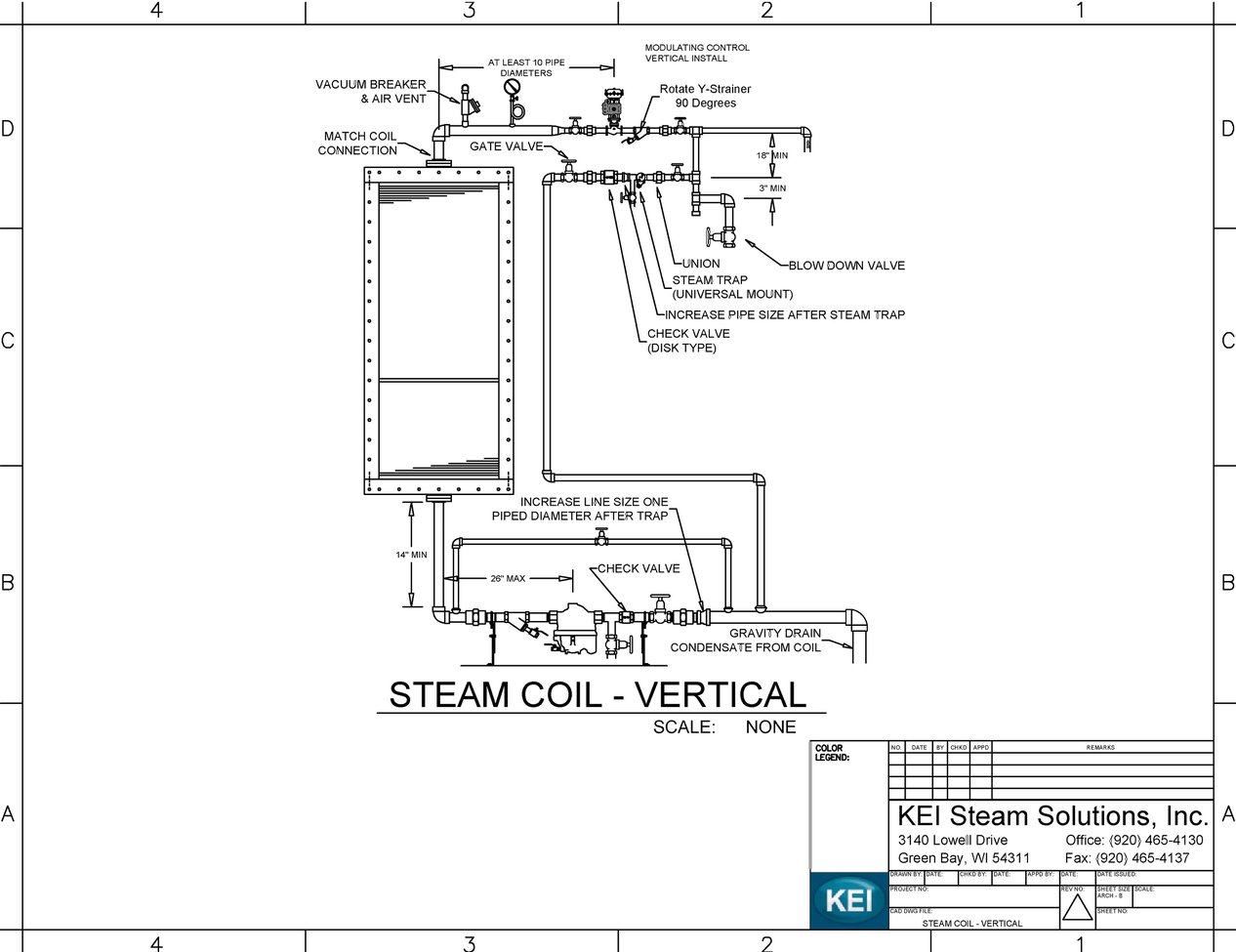
Vertically oriented steam coil schematic, courtesy of KEI Steam Solutions, Green Bay, Wisconsin.
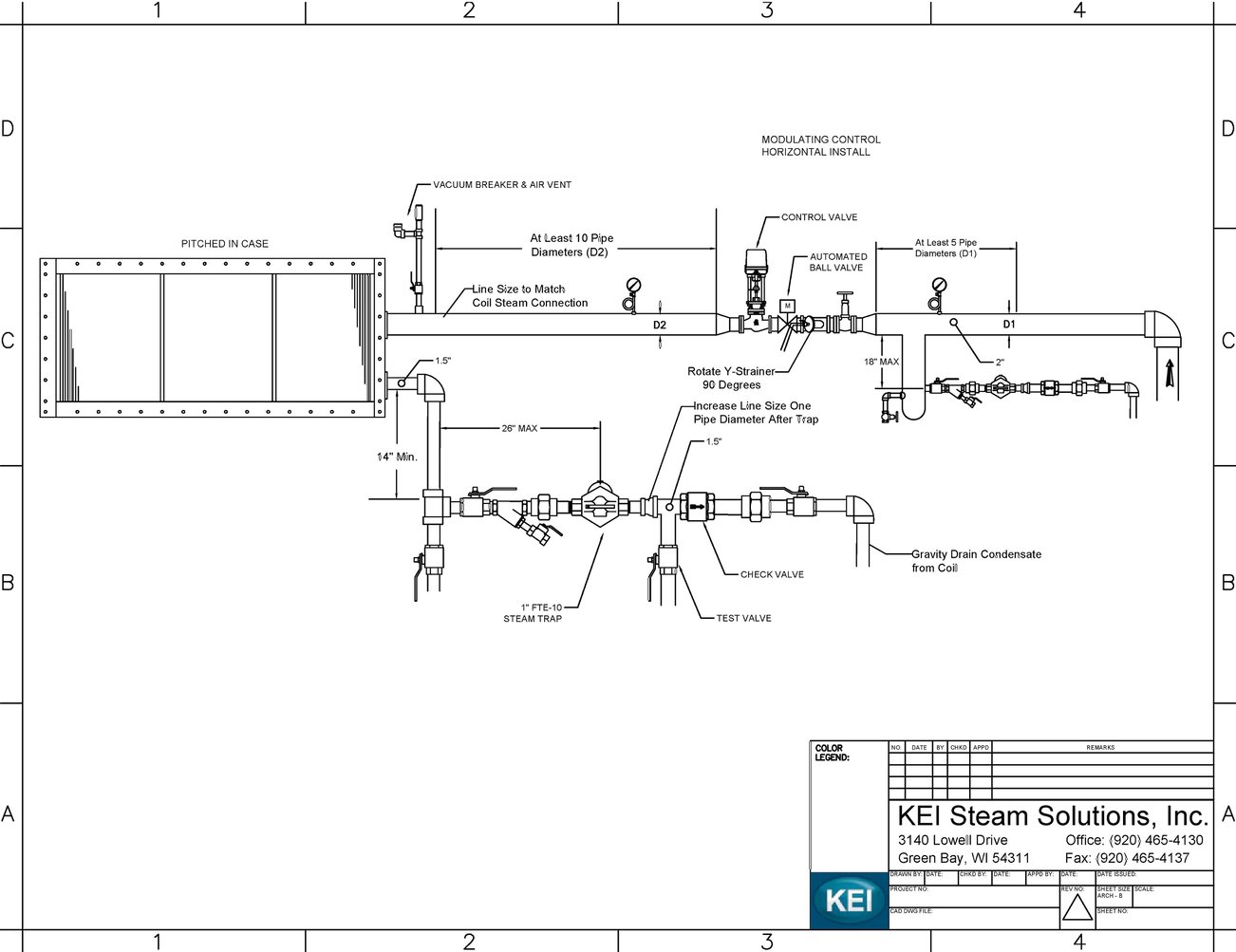
Horizontally oriented steam coil schematic, courtesy of KEI Steam Solutions, Green Bay, Wisconsin.
-
In all steam coils, it’s beneficial for steam to be distributed into the coil’s circuits as evenly as possible. This design will often include orifice stubs or a baffle inside the inlet header to prevent uneven loading.
-
Single-pass designs are usually seen in applications where the inlet air temps are above freezing. But this design provides excellent freeze resistance when installed vertically. To realize this benefit, we recommend keeping coils’ finned lengths to less than 72 inches and steam pressured maintained at 5 PSIG and above.
Multi-Pass Standard Steam Coils
-
Multiple-pass steam coils are typically used for applications where it’s beneficial to have the connections located on the same end of the coil.
-
Usually, multiple-pass designs are only used when:
a. Spatial constraints or some other factor precludes the use of single-pass design.
b. More than two rows are needed to meet the application's requirement and all rows must be contained within a single casing.
-
When using multiple-pass steam coils in sub-freezing conditions, constant steam pressure and temperature is especially critical. This is due, in part, to the longer circuit lengths found in multiple-pass designs, which, when coupled with the fact that these designs cannot be sloped, can inhibit condensate removal, and increase the potential for freezing.
Steam Distributing Coils
Steam distributing coils are more complex than their standard counterpart, due to their header design. Sometimes called “tube within a tube” coils, steam distributing (SD) coils feature headers featuring just that – a smaller tube encased in a larger one.
The intent of the tube-in-tube design is to facilitate a more even distribution of steam from the outer tube into the rest of the coil. This design also contributes to more uniform air temperature coming off the coil, which allows for better temperature control for applications involving low or variable steam pressure.
Single-Pass Steam Distributing Coils
As with standard steam coils, single-pass steam distributing coils feature connections located on opposite ends of the heat exchanger.
Steam Coil Design Best Practices
When designed properly, steam coils can be extremely efficient. To best realize that efficiency, there are some important considerations to make regarding the heat exchanger’s design. We’ll cover some design best practices for the following steam coil components:
-
Type of coil construction (plate fin or spiral wrapped)
-
Tubes
These apply to both standard steam and steam distributing coils.
Type of Coil Construction (Plate Fin or Spiral Wrapped)
With steam coils, most of the energy transfer occurs at the fin surface, so choosing the right material, design, and type of fins are all important considerations. And all these decisions require balancing tradeoffs to best meet the requirement of your specific application.
Step one is to select between a plate fin or spiral wrapped design. The linked article explains in more detail, but the high-level advantages of each are below.
Advantages of a Plate Fin Design
-
More variety of material options
-
More variety of fin surface configuration options
-
Potential for better heat transfer performance through greater surface area
-
Greater variety of fin density options
-
Superior cleanability of the fin pack
Example of a plate fin steam coil
Advantages of a Spiral Wrapped Design
-
Potential for easy replacement of tubes
-
Individual tubes can be outfitted with differing patterns.
-
More options for fin thicknesses
Example of a spiral wrapped steam coil
Cleanability should be factored into your decision between the two as well. Unless your steam coil is operating in a clean room environment, particulate, dust, and other debris will inevitably accumulate on the fin surface over time, a phenomenon called fouling. The impact of that layer of grime isn’t just aesthetic, as it reduces the heat transfer capacity of the metal and can dramatically lower performance.
Design choices to account for this factor should be a balance between preventing dirt and grime and cleanability when it does occur. Some things to consider as far as cleanability are:
-
Plate fin designs typically accumulate less debris as they usually have fewer leading edges.
-
Wider fin spacing means less opportunity for debris to accumulate and bridge to adjacent fins.
-
Thicker fins (.010”+) should be used if cleaning procedures include pressure washing.
-
As with fin spacing, the potential for fouling can be reduced by using fewer tubes when possible.
Tubes
In a vacuum, the most effective tube material from a heat transfer perspective is copper, and it’s best practice to use it when possible. But with steam coils, copper’s not always the best choice. Like with fins, the decision comes down to priorities.
In many steam systems, corrosion is often more of a concern than tube-side heat transfer, so it’s common for that to be the guiding factor in tube selection. Corrosion-resistant materials like stainless steel can be used, or less-corrosion resistant materials can be enhanced with some type of anti-corrosion coating.
Some steam systems operate at high pressure, a factor that must be accounted for during tube selection. For outer tubes on steam distributing coils, we’ll typically recommend an OD of 5/8”, 7/8” or 1”. For standard steam coils (and inner tubes on SD coils), we generally recommend using .035" tubes for applications with lower operating pressures (<50 PSI) and .049" for pressures above that, but this is more of a rule of thumb or starting point than a hard and fast rule. Every application is different and tube selection demands case-by-case scrutiny.
How SRC and KEI Can Help You Optimize Your Steam System
Steam is a unique heat transfer medium. Unlike single-phase working fluids like water and some refrigerants, steam is a two-phase fluid. This is one of the primary traits that can make steam tricky. True steam expertise comes only from practical experience over time. And that's where SRC and KEI's unique and comprehensive steam expertise can help.
Super Radiator Coils has built steam coils for nearly a century for commercial and industrial markets. And, in our partnership with KEI Steam Solutions, each of us are able to focus on what we do best. With Super Radiator steam coils providing the heat transfer, KEI can help optimize other areas of your system. We'll make sure your coils perform as required while also ensuring the entire system is functioning as it should. Whether that's condensate trap selection and sizing, valve sizing, or even training your team on the specifics of steam, we're here to help you get the most from your equipment.
More About KEI Steam Solutions:
KEI Steam Solutions, Inc. provides complete end to end solutions for steam, condensate, and fluid systems. KEI commitment is to provide the highest quality products, technical support, engineering, and service to our clientele. We offer the one stop shop for the Process, HVAC, Food & Beverage, Industrial, Refining, and Power markets in the Midwest. If you're interested in learning more about how KEI and SRC can optimize your steam system, request a quote with KEI or get in touch with SRC.
Don’t get left out in the cold when it comes to heat transfer information. To stay up to date on a variety of topics on the subject, subscribe to The Super Blog, our technical blog, Doctor's Orders, and follow us on LinkedIn, Twitter, and YouTube.